A newly installed CNC brings Micron’s vision of standardization to full fruition.
The new machine — a Citizen Swiss lathe — expands Micron’s production capabilities and versatility. It increases the longevity and performance of our fleet. What’s more: it’s a final move within a long-term plan to upgrade and standardize our equipment.
These upgrades reflect Micron’s continuous improvement goals, which in turn benefit our customers.
CNC turning versatility
Micron’s combination of Swiss and conventional CNC lathes means we can deliver a wide range of options to our customers. We think of this versatility in terms of diameter size, overall length, material, and complexity of the part.
Micron can turn parts 2″ in diameter and smaller from bar stock or can hand load rounds up to 3.5″ in diameter. Our use of Swiss-style CNC lathes, such as this new L32, offers advantages in turning longer parts with greater accuracy and precision.
The new L32 can run bar stock up to 32 mm (1¼”) in diameter or smaller. This is a size up from the 20mm machine it replaced. The change increases our production capacity for the larger diameter parts — a range where we find high demand. But because it can run smaller stock too, we don’t sacrifice any capacity in the smaller diameter ranges.
The standardization journey
Standardization of equipment has been a long-term goal of Micron that has informed several key machine sales and purchases. These include the recent sale of our Mori Seiki and purchase of a Miyano in addition to the replacement of our 20mm Citizen with the 32mm Citizen.
By having the right combination of machinery, we’re able to reduce training time and improve knowledge retention among our production team. Common tooling across our machines creates opportunities for faster lead times and lower production costs. Additionally, most of our machines are now serviced by a single distributor.
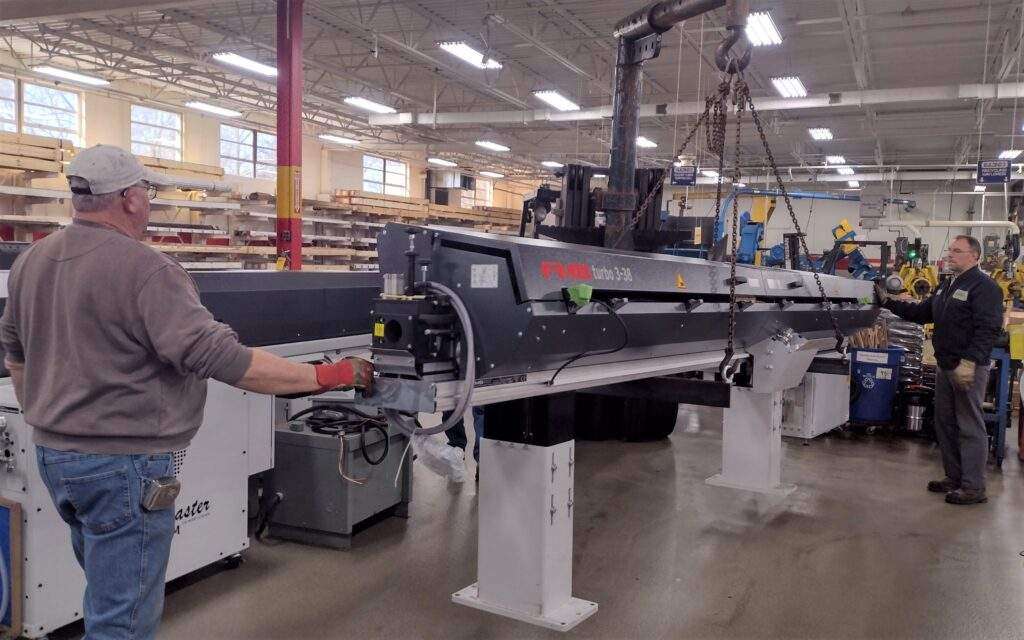
A great machine
Machinist Dan “Ski” Szczepanski says the new machine is a nice upgrade.
According to Dan:
“The L32 is great because it’s spacious inside the machine. That makes changing tools and removing debris pretty easy.” Additionally, he says, “the newer machine works with a different type of bar loader that’s much better than the old one.”
Aside from the specifics of this purchase, upgrading our CNC equipment always feels good from the perspective of a precision machining shop. Being able to re-invest in our production capabilities reflects our hard work and success over past years and a commitment to grow and improve in the future.
With any luck, this great addition to our shop will provide many years of service to us and our customers.
Recent Comments