Robin Thomas — a quality control technician and Micron employee of 30 years — recently retired.
We celebrated her contributions at Micron with a luncheon, where we met some of Robin’s family and enjoyed the company of other retired Micron employees who came back to welcome Robin to the club.
Robin is looking forward to enjoying the outdoors. She plans to plant a garden, raise chickens, and spend lots of time with her children and grandchildren.
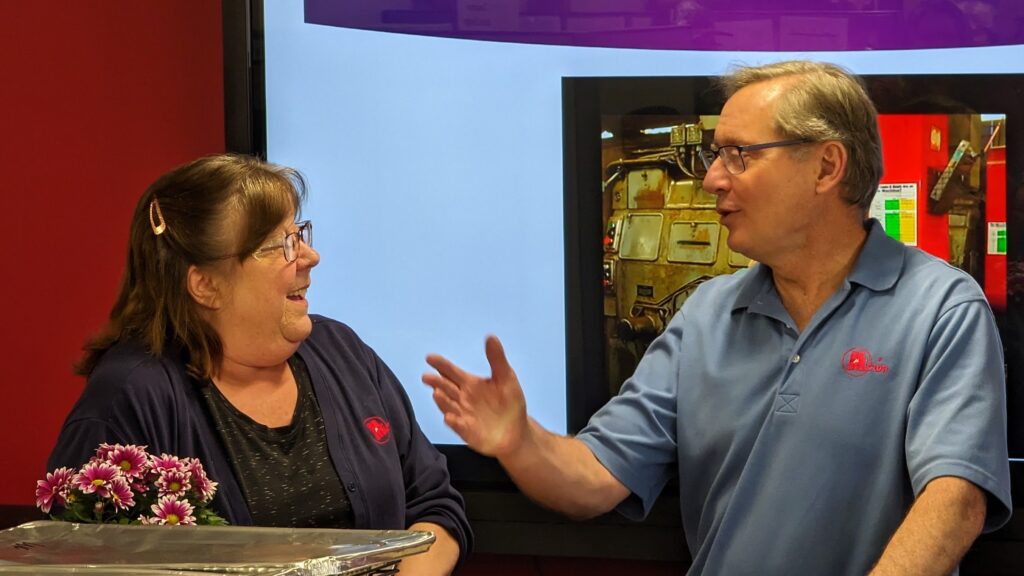
A team player
Robin is know for many things — a quick wit, being able to “keep the guys in line” — but one observation that persisted was of her desire to help others. As quality manager Brian Hoff noted, Robin frequently helped sort parts, going beyond her duties in the quality department. And this was just one of many ways Robin was willing to lend a hand. Over the years, she went above and beyond to help us meet deadlines, solve problems, and improve. The fact that she cares about her coworkers and the company is evident.
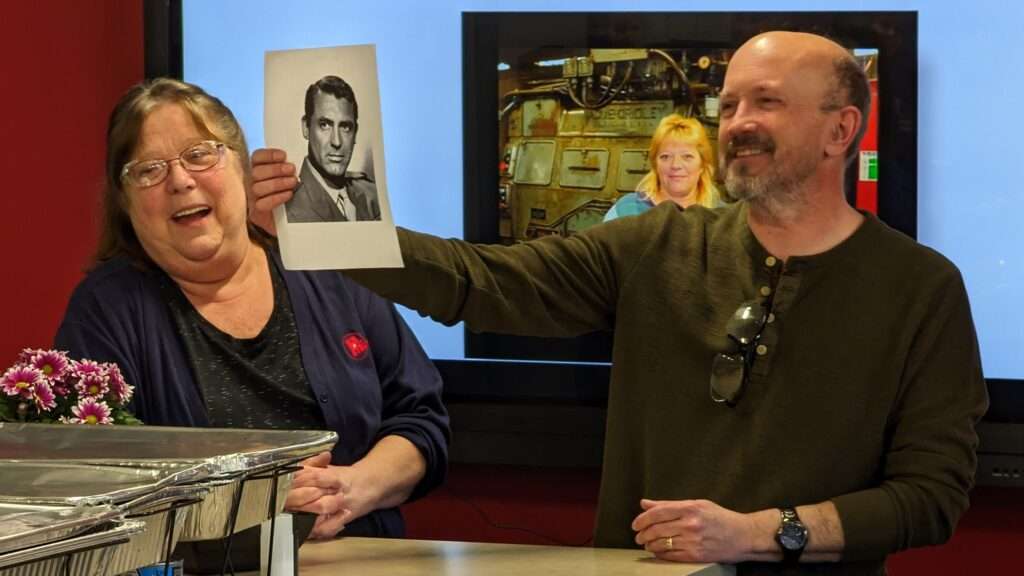
We’re extremely grateful to Robin for her years of dedication to Micron.
Fortunately for us, her smiling face will be back in the shop again soon. Ever the helper, Robin has volunteered to come back on a part-time basis — so we’re looking forward to seeing her again after a well-earned vacation.